Stuart
and others, greeting from NZ......a friend and myself have
been playing with a similar thing to what you describe.
A 400 electric motor spinning at
9,000rpm on a ballrace sliding double rail system, then thru
a meter reading WATTS , all coupled to an electronic set of
scales. Power for this thing is thru a 12 volt car battery.
my scanner is currently down but I'll put a photo Stu in the
mail to you. Interestingly you and I seem to be on similar
tracks. A typical F3d prop produces 324 grammes pull, 162
watts, at 9.000 rpm. I use this machine to allow me to make/
finish F3d props and although not running at 30,000 rpm as
typical to an f3d motor certainly making the props the same
at 9.000 must go along way to having similar/ same props.
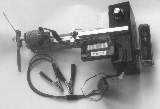
Click
to Enlarge
How this little machine came about
was because I do not have access to CNC milled prop moulds,
and as you know 'repeat props' on Aluminium filled epoxy moulds
cannot be guaranteed to be the same, the moulds do move so
I decided in conjunction with an electronics friend to put
together the little toy that would enable me to 'work propellers'
( read file and sandpaper) that would give me similar results
i.e thrust, wattage at a 9,000 RPM. Its purely a system that
I can get a comparison of before and after.
Spinning the motor at 9,000 allows
me to read off the wattage and thrust which I can then compare
to a 'known working prop'- I've been playing with the HARVEY
WESTLAND prop and although only reading to 9,000 RPM on this
toy, surprisngly over three flying props the ground RPM was
darn near the same 27,800 - 28,300 and the radargun gave results
all within 3.5%. Whilst it maybe a crude way of doing things
it certainly now has given me a system that will give me props
that produce the same trust and wattage draw- the inference
to me therefore is that they would then be similar 'behaving'
propellers.
There are possibly better ways
of doing things but even after playing with a Prather pitch
gauge and Vernier calipers I could never be assured of the
props giving the same results.......this has solved the problem!
If you have a close look you will see a rubber band in a triangular
format over two bobbins/ buttons which is a very satisfactory
way of bringing the aluminium sliding bar, which is ball race
mounted, back to a zero reading on the electronic scales.
The whole thing gets mounted into my bench vice.
I'll ask my electronic mate about
electric motor efficiency- he is a bit of a boffin and maybe
able to advise on your electric motor problems including 'shaded
pole'. Will advise within a couple of days. If you want I
can do a drawing of the whole system.
Trevor Henderson,
Henderson Design Ltd.
bigtrev@xtra.co.nz
|