Have I got a treat
for you this month! The idea for this month's topic comes
from Bruce De Chastel, up dere in de Sunshine State. If you
don't know Bruce, not only is he a very talented pylon flier,
but he's a very sharp cookie indeed. The only problem is that
he makes props in competition with me, so we don't often get
to swap ideas. On this occasion I was complaining about the
problem of converting a favourite propeller to CNC coordinates
on the milling machine.
You all know how I feel about prop airfoils, from my previous
efforts in ACLN. Often the only way to improve a prop is to
make sure the airfoils are the right shape, whatever that
is. If you want to compare props, you need to know the camber
and camber high point to determine the zero-lift angle and
hence the experimental pitch. Now these two variables are
hard to pin down with any accuracy: they are just plain hard
to measure. Well Bruce had the answer to this, and in an unguarded
moment shared it with me, so old big-mouth me is now going
to tell you.
This is what you do. Borrow a prop. Cut a slice
out of the prop; say a mm wide. A good place to start is at
the 3/4 radius point on the blade, as this is representative
of the way the whole prop behaves. Drop it on the platen of
your computer scanner (mine is an Optic Pro 9630P) and scan
it at a resolution of say 300 dpi. The result is stunning.
That tiny airfoil can be blown up to 6" wide, where all its
imperfections and graces can be examined.
Even more stunning, my "MicrografX Photo Magic"
software lets you put a ruler over the image. In fact, You
can put an arrow on the edge of the profile and the screen
shows the co-ordinates of the section at that point accurate
to 50 microns! You can even select "View/Info" and the co-ordinates
are displayed neatly to the side of the screen. With these
data, you can get the high point and camber very readily,
with all the accuracy you ever dreamt about.
Well, I couldn't wait. 6 destroyed props later,
I had six little airfoils sitting on my scanner platen, with
the P100 warmed up and ready to go. The first scan was not
too good. It had big shadows on one side, and the Tornado
yellow nylon did not show up so good. The airfoils were re-arranged
so that they pointed down the platen, after they were coloured-up
with black Texta (all except the APC). This time the results,
with the contrast turned up a bit, were really pretty good.
There should be a copy of this scan somewhere near this bit
of text. Take a quick peek at it. I'll deal with the results
one at a time.
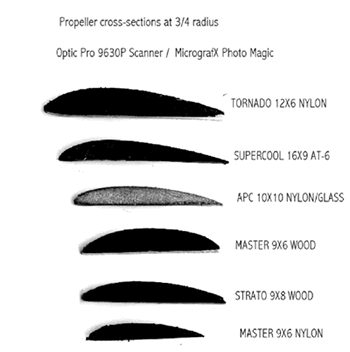
The Tornado 12X6 airfoil is really very good,
much like Clark Y. If anything, it may be a bit too thick,
but that is forgivable in a nylon prop where strength is a
consideration.
Next is one of my CNC aluminium moulds, a pylon
prop for the AT-6 Texan/Harvard 1.2 cu.in. class. Prop is
carbon-fibre, you can find it on my Website at www.space.net.au/~props.
The airfoil is NACA 6311. The 6 means the camber is 6%, the
3 is the high point at 30%, and the section is 11% thick.
This is what is called a "NACA 4-digit section". The thickness
form is that of Clark-Y, although it has been thinned a little,
as Clark-Y is 11.75% thick. The thing that is interesting
about this airfoil is that the high point has been moved forward
to 30% (Clark-Y is at 40%).
The forward high point has the same effect as
leading-edge flaps, or the droop-snoot type of airfoil. This
feature allows the airfoil to generate high lift at high angles-of-attack,
very useful where good acceleration is required, such as in
F2C, F5B and F2A. The scan shows that it has been reproduced
faithfully, as you might expect from a machine accurate to
5 microns.
The APC prop is next. It appears to have a circular
camber line, which puts the high point quite a long way back.
It reminds me of Go795, an excellent low drag airfoil, but
not so good lift-wise. It is not really the section you would
choose for a propeller, but its accurate profile is going
to guarantee better performance than most hand-shaped airfoils.
Last month I mentioned some props had the airfoil
on backwards. That is the case with the Master Airscrew 9X6
wood, although I am not sure I would really call this an airfoil.
It felt bad slicing up this prop, as it was a beautiful piece
of timber, well lacquered and most attractive. But it didn't
feel so bad after I saw the section, glad I never put it on
an airplane.
The Strato 9X8 dates back to the 1950's, an
Australian-made prop of good quality, very popular at the
time. Paul Turner used Strato 10X5's on his OS Max 3 powered
Thunderbirds, so I did likewise. Problem was my Max 3's never
ran as well as Paul's, to this day I wonder what his secret
was. The trailing edge is a bit thick, as you will find this
with nearly all wood props, including the full-size variety.
It is simply a strength matter; thin wooden trailing edges
are vulnerable to handling and usage damage. Otherwise, this
is a good section, Clark-Y with a bit of extra forward camber.
The improved performance of aluminium alloy
props, or in our case nylon and composite, is almost entirely
due to the thinner trailing edges and thinner sections these
materials make possible.
Contrast the Master 9X6 nylon with its wooden
counter-part. The section is well suited for props, and Master
Airscrew nylon props deservedly have a very good reputation,
despite their homely appearance.
Well there you have it. Is that a neat trick
or is it not? To a single-minded fellow like myself, it is
very exciting indeed. Time to sign off. To you chaps who have
recently been kind enough to comment favourably on my series
of articles in ACLN, I thank you. The rest of you can go .....
oops, not that, Rosemary has told me I must change my image! |