The properties of
wings and propellers are strongly influenced by the shape
of the airfoil sections selected by the designer. Perhaps
the most well known section of all time is Clark-Y. To quote
Ron Warring from his book "Airfoil Sections", price
2 shillings in 1946:
"This is one of the most popular sections among modellers
all over the world, and is also used as an airscrew section.
It has the advantage of making a wing easy to construct, and
the performance has all-round merit. "
Cl maximum is 1.42 for full scale work, and
1.25 for model work. Cd minimum for an aspect ratio of 6 is
.0183. L/D maximum is 17.2. The angle of zero lift is -5.4
degrees. " Well, they were in 1946!!
To paraphrase the late Western Australian champion
modeller and sailplane pilot Len Armour,
"In turbulent flying conditions, Clark-Y is as good or
better than modern laminar flow sections"
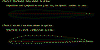
Food for thought. So much so, that the National
Advisory Committee on Aeronautics (NACA) based its 4-digit
family of wing sections on the thickness form of Clark-Y and
Gottingen 398, these sections being known for their high efficiency.
The relative ease with which these sections may be generated,
being expressed as simple formulae, also makes them attractive
for use in propellers made in CNC machined moulds.
A concern has developed in my mind that the
Formulae for NACA-4 digit sections may have problems. First,
let us look at the trailing edge of Clark-Y. According to
R.H. Warring, the thickness of the trailing edge as a percentage
of the chord is 0.12. Soartech 8, "Airfoils at Low Speeds",
by Seelig, Donvan and Fraser, has a thickness of 0%.
Taking the Soartech 8 values for Clark-Y, i.e.,
thickness to chord ratio of 11.72%, camber of 3.55% and camber
line high point somewhere around 35 to 40% of chord, the NACA
4-digit formulae yield a trailing edge thickness of 0.123.
Close to Warring's value, and not at all like Soartech 8.
The NACA formulae also yield a maximum thickness-to-chord
ratio of 11.7234%, not the same as our desired value of 11.72%.
Well, shock, horror!! It is hard to see anyone
losing sleep over these tiny percentages. NACA should be congratulated
for doing such a great job in pre-computer days (which is
also where your scribe comes from. My first job, as a mathematical
statistician, had some real perks. Like Jenny, Erica and Jill,
whose job it was to do all our calculations on electromechanical
calculating machines!). OK, so maybe we can live with the
trailing edges and thicknesses. The errors are small.
But what happens at the leading edges? Well
you might ask, for therein lies the problem, and it is very
real.
To obtain the full NACA 4-digit airfoil section,
the Clark-Y type thickness form is wrapped around the NACA
4-digit camber line. Using the method as described in Abbott
and Von Doenhoff, "Theory of Wing Sections", something
alarming is seen happen. To quote from page 113 of that illustrious
book: "This method of construction causes the cambered
wing sections to project slightly forward of the leading edge
point".
Well hang on now! What are we saying here! You
mean the leading edge is not at the coordinate (0,0) ! Not
only that, but the forward point of the camber line does not
intersect the leading edge? Whoa, this is a bit extreme folks.
No way. Not on.
So why the panic? Well folks, my propeller design
algorithms are all based around the experimental pitch. This
is essentially the pitch at which the propeller produces zero
thrust: it is the pitch measured against the zero-lift line
of the airfoil. The datum for the zero-lift angle is the chord-line,
defined as THE LINE JOINING THE MOST FORWARD AND MOST REARWARD
PARTS OF THE WING SECTION. Now we find that, not only is the
NACA equations a bit off for the trailing edge point, it is
also badly off for the leading edge.
The datum line of the airfoil, the chordline,
does not lie co-incident with the NACA 4-digit datum line.
The equation I use for the zero-lift angle is that suggested
by R.T. Jones. With M the camber, and P the position of the
high point on the camber line (just as required by the NACA
formulae), the zero-lift angle is given by:
Zero-lift angle = ATN(M/(1-P))
where ATN means inverse TAN, and the Zero-lift
angle is in radians.
Due to Reynolds number effects, I usually apply
a small correction to match the flight regime that I'm using.
In the case of Clark-Y, Soartech 8 gives the zero-lift angle
for Clark-Y at Rn = 99000 as -3.6 degrees. The value calculated
from the NACA input values is -3.386. Correction by a factor
of 3.6/3.386 is indicated for this low Reynolds number. The
correction will be less at higher Reynolds numbers.
But what happens when we take the datum of the
true chordline into account? There is an angular difference
of 0.169 degrees between the true chordline and the NACA datum
line for the camber and high point. Thus the true zero-lift
angle is reduced by that amount, to yield a zero-lift angle
of -3.217 degrees. The correction is now 3.6/3.217 or a factor
of 1.119, a nearly 12% error. Not so good.
But it gets worse. Sometimes one does not want
to use Clark-Y.
I have always been impressed with frontal shots
of the Hellcat US Navy fighter. The wing section seems to
be thick with a forward high point. I guess if you were trying
to land a monster like that on a pitching carrier deck, you
might like a wing that would fly slowly at high angles of
attack without stalling, so that might be a good way to go
with the wing section.
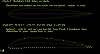
Lets assume that the thickness is 15%, with
the highpoint at 30%. The camber will be something like half
the thickness, say 7%. Then the error becomes 0.519 degrees,
a 10% error in the datum angle.
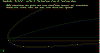
How about the old Dixielander NACA 6409 section?
The error in datum angle is 0.162 degrees, a 3% error.
On my propellers, I like to run thick sections
near the root so the blades don't snap off. My latest Berserker
F3D prop uses a 21% thick root section, camber of 11% and
high point at 33% of chord. Not a very effcient section, but
one demanded by the strength of materials and the loads involved.
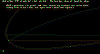
The error in datum angle for this section is
1.120 degrees, an error of 13.7%
Finally, there is one other problem. The chord length measured
along the NACA datum is less than the true chord length, measure
from leading edge to trailing edge. This is the result, again,
of the method of construction of the NACA 4-digit sections.
The error for Clark Y is .022%, and for my Hellcat section
is .678%
For further reading, or to calculate your own
4-digit sections, you need to get your own copy of Abbott
and Von Doenhoff . If you are serious about aerodynamics,
you must have it anyway. There is a review of this book on
my website at www.supercoolprops.com.
You can also order the book through my website
and from Amazon.com.
Well I guess this all seems a bit esoteric to
the general dogsbody's that read my rubbish. But in my former
life as a Nuclear Standards Scientist, my peers would have
relished having me hung, drawn and quartered for errors of
this magnitude. For those of you born after the Medieval age,
"hung" means dangled from a rope by the neck until
almost dead. "drawn" means having your guts pulled
out through your belly-button, and "quartered" means
torn apart by 4 horses going in mutually exclusive directions.
That is where the breed of "Quarter" horses got
their name. Anyone wanna buy a bridge? |