My
regular readers may recall my obsession with overcoming the
engine problems of my delinquent youth. Perhaps I should say,
middle age, as these engines were typically produced in the
1970’s. This is a progress report bearing on piston/cylinder
fits.
The engines in question are the ST G21/46,
Enya 45 I 6001 and Enya 45 II 6002. Diamond lapping the rings
in the ST G21/46 and Enya 45 I 6001 produced very good results.
The above mentioned Enya 45’s have very similar intake,
transfer and exhaust timings to the Super Tigre engine: This
has led me to puzzle why the Enya’s as supplied did
not run with the superb ST 46 burble.
The folklore goes something like this. The
Enya 45 6001 was popular with stunt fliers in the early 70’s:
the 45 6002 was not up to scratch for stunt and had therefore
been changed to suit R/C fliers, while the ST46 remains the
yardstick by which to judge more modern engines. Well, in
view of the timings I have measured, none of this really makes
sense. Since I also have a dud ST46, there must be some underlying,
dare I say intransigent, factor at work. Further, the observation
was made that ringed motors are run out as soon as they are
run in! (non-Dykes).
As noted above, lapping the rings to improve
compression seal was a great step forward: indeed the Enya
6001 now does run with a superb rich burble, thereby validating
my hypothesis concerning the way these motors run. The tendency
of these motors to go lean and stay lean has been eliminated,
the engines breaking back rich after manoeuvres with a satisfying
regularity.
Well with all this joy bursting out, it was
time to bring out the Enya 45 6002. This engine had been zero-timed,
thanks to the unbelievably fortuitous circumstance that Model
Flight in South Australia had in stock a new piston/cylinder/ring
set, which I hungrily snapped up. This for an engine that
came out in the mid-70’s!
I gave it 45 minutes on the running-in stand,
put it in the beat-up old Firecracker, whereupon the joy-bubble
promptly burst. The run was unbelievably bad: un-tuneable,
poor power, sagging power, RPM everywhere. This was essentially
a new motor: how could this be happening to me? My previous
life must have been sinful indeed.
Resisting the urge to duck out to the shed for
a quick diamond lap, the time to set the old mind into gear
appeared to have arrived. Nothing much happened, but a chink
in the corner of my poor stroke-addled, tinnitus riddled brain
was screaming “piston/cylinder/ring fit”. Well,
if I were not to do the lap, what was the right course to
take? Would it be possible to find the problem by actually
measuring the shape of, say, the cylinder? Many years ago
I had mounted a Rossi 15 cylinder in a lathe chuck, with a
dial gauge mounted on the tool post. This particular dial
gauge had a little finger sticking out of it, so it was indeed
possible to measure the bore taper in the Rossi.
Well, I have a nice new lathe, but lack the
dial gauge and funds to buy one. Was there another way? Would
I ask this question if there were not? Dear reader, this in
not an attempt to insult your intelligence, just an attempt
to indicate the slow and torturous way my brain works. Remember,
this is all happening 30 years too late to be of any help
to my competition record!!
My CNC milling machine is essentially a giant
3-dimensional micrometer with digital read-outs. The spindle
normally holds a cutting tool, but there is no reason why
it should not hold a finger, just like the dial gauge. The
position resolution of the machine is .005 microns in each
of the 3 axes, which is about 0.2 thousandths of an inch.
Hopefully, this would be enough: in the event, barely, but
better than nothing.
So the Enya 6002 cylinder was mounted vertically,
flange down on a piece of perspex, as shown in the photos.
The required finger was machined up out of brass, with extra
diameter at the measurement point. My multimeter has a setting
which goes “beep” whenever the probes are placed
across a low ohmic resistance, so one probe went to the finger,
the second to the cylinder. By moving the spindle down, the
finger could be made to find the bore at any given depth,
simply by moving the finger sideways until the meter went
“beep”. This procedure worked splendidly, so that
after an hour of measuring the bore front to back and transfer
to exhaust, I was able to make some observations.
Between top-dead-centre (TDC) and the exhaust
ports, the bore was out-of round by 0.8 thou. There was no
(detectable) bore taper front to back, but 0.4 thou taper
across the ports. Below the exhaust ports, the cylinder was
0.4 thou out of round, with taper front-to back of 0.7 thou
and 0.4 again across the ports.
What did these numbers mean? These are small
dimension errors: could they cause the motor to run badly?
One assumes the cylinder was intended to be perfectly round,
with no tapers. In this fashion, the ring could be expected
to seal, even though it is not pinned and does rotate while
the engine is running. Further, with no taper, the ring would
not need to expand and compress with every stroke: surely
desirable.
Not having a clue myself, it was off to see
the Oracle at Delphi, or should I say, the Cestone at Gosnells
(aka Charlie Stone, model engineer and aeromodeller extraordinaire!).
Charlie has been battling with piston rings himself, as Norm
Kirton, like myself, tries to restore the glories of his (Wharfdale)
past, viz getting the ETA 29 back up to 120 MPH, as was done
so readily 50 years ago. Charlie has some nice machines, including
a filing machine, an item I had never heard of before, but
which I instantly desired!
His work included trade secrets, which I cannot
divulge here. However, he was able to describe to me the means
and principles of honing cylinder bores, in sufficient detail
to frighten me off from such a demanding task. In my fantasy
world, I had planned to machine up a hone on my nice new Taiwanese
lathe. Having spent half a day trying to get the swarf out
of the geared head oil bath, I really needed a project to
justify the frustration plus the $4200 expenditure. However,
I was further disillusioned by Ian Thompson, silver medallist
in Aussie team place F2C at the recent (2006) Spanish W/C,
when he asked me if I had lined up the spindle with the lathe
bed. You mean they sell them not in alignment?
This was starting to get embarrassing, when
Charlie dropped the name of F2B/F2C guy Richard Morrow.. Very
kindly, he invited me around to his factory, wherein were
no less than 7 honing machines.
Whistling bravely, with my hands firmly placed
inside my pockets, I wandered in. There was this huge hydraulic
cylinder, being firmly and repetitively penetrated by what
looked like a large sex machine. Evidently this is called
“honing”, but I do know other words for it. Dick
wandered up to greet me, so I shook his left hand and we got
down to business. This was a man who knew honing. He even
had tiny little hones for making gudgeon pin holes, so it
was time to listen and keep my thoughts to myself.
Producing my miscreant Enya sleeve, I passed
it to Dick who proceeded to look it up and down, round and
about, in a manner I can only describe as disgusted. Eventually,
he went to his Delapina honing machine, installing the appropriate
Sunnen hone: with the hone turning at 300 RPM, and the cylinder
drenched in what looked like treacle but which I assumed to
be honing oil, he proceeded to improve on Mr. Saburo Enyas’
factory product.
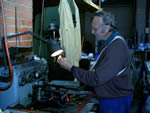
To cut a long story short, on re-measurement,
the cylinder had indeed changed its dimensions. Above the
exhaust, the out-of-round had reduced to 0.2 thou, an improvement
by a factor of 4. The taper in both axes was reduced to nothing.
Below the exhaust, the out-of-round had increased slightly,
while the tapers were basically unchanged.
Hopefully, the “above exhaust”
measurements were the important ones.
So I reassembled the motor, without touching
the ring. No point changing 2 variables at once: the idea
was to see how important the bore was, and by what amount
the out-of-round needed to be reduced.
With the engine on the test stand, I was somewhat
alarmed to find it had no compression worth mentioning. Hand
starting was not going to work, so I hit it with the electric
starter. Stopping it after 5 minutes of very rich running,
I found good hot compression, which was rewarding. After a
further half-hour, with the compression fully restored, into
the model and off to Whiteman Park. Sure enough, the motor
ran beautifully, including the Super Tigre burble.
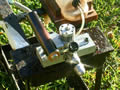
Draw your own conclusions on all this. But
here are some useful snippets. Dick has a Mitutoyo bore gauge:
if I heard him right, it reads down to 1 micron, which is
down where you need to be for model engines. The gauge is
useful, but I got the impression that honing is largely done
by “feel”: that must mean the human hand can detect
movements less than 1 micron. Clearly my next step was to
buy my own hone. This idea didn’t get far; the starting
price for a Sunnen hone assembly is $1000. With ringed motors
such as these, the bore is parallel. How you would ever control
the honing of tapered bores, I cannot begin to imagine.
So there you have it. Watch this space.
Addendum: Seems I'm not an
orphan re piston/cylinder/ring fits. This is what Bill Werwage
had to say in Flying Models, January 1980, on engine performance
in his "Juno" article.
"Much emphasis has been on trivia. Little on the fact
that most of our current motors don't have a proper ring seal.
Certain engine cylinders on the market now should be against
the law and a reward posted for missing, good rings. Sometimes
I feel as though I am more in competition with the machinery
and people at the factory than the other competitors.
These motors are fine with their stock bearings, and stock
just about everything else too. However, a good ring seal
that lasts any length of
time is truly rare." Amen to that.
|